TÍNH TOÁN KHỞI ĐỘNG SAO – TAM GIÁC
A complete Electrical Engineering portal
Star-Delta starter design tool | Wye-Delta starter design tool
Star-delta starters are widely used for starting three-phase induction motors. It can reduce current inrush to 1/3 of direct-on-line starting current. Here is an advanced Star-Delta starter design tool that will help you select the optimum current rating of contactors, fuses, and circuit breakers (MCB, MCCB) for a star-delta starter circuit.
Online star-delta starter design tool
Motor data input
Enter the motor rated voltage | |
Enter the motor rated power | |
Enter the motor Efficiency | 95% |
Enter the motor Power factor | 0.85 |
Calculated Values |
|
Motor FLC | A |
Motor Starting Current | A |
Output
Star-Delta Stater rating |
|
Required fuse rating | |
Required Thermal Circuit Breaker rating | |
Main contactor current rating | |
Delta contactor current rating | |
Star contactor current rating | |
Overload Setting* | |
*Overload relay is located between the main contactor and the motor. |
Looking for a Star-Delta starter wiring diagram? Find it here: Star-Delta starter wiring diagram – Control and power wiring diagrams
How to use the Star-Delta starter design tool?
The above tool requires the following data for calculation:
- Motor rated power in HP or kW. (Mandatory)
- Input supply voltage. (Mandatory)
- Motor Efficiency as per nameplate – (if known).
- Rated power factor (if known).
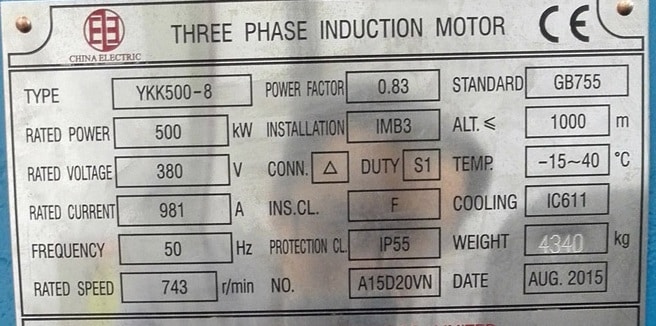
Learn More: Star-delta starter (Wye-Delta Starters) – Circuit, working
After entering the required data, click on the “Calculate” button to find out the required fuse rating, Circuit Breaker rating, contactor current rating, and overload setting. This tool can help you to select contactor for star-delta, Overload relay, and MCB or MCCB for star delta starter circuits.
Large induction motors, when started directly on line, draw very high currents. Therefore star-delta starters are widely used for motors rated over 10hp or 7.5kW (even small motors can be started using the star-delta method). This can reduce current inrush to 1/3 of direct-on-line starting current.
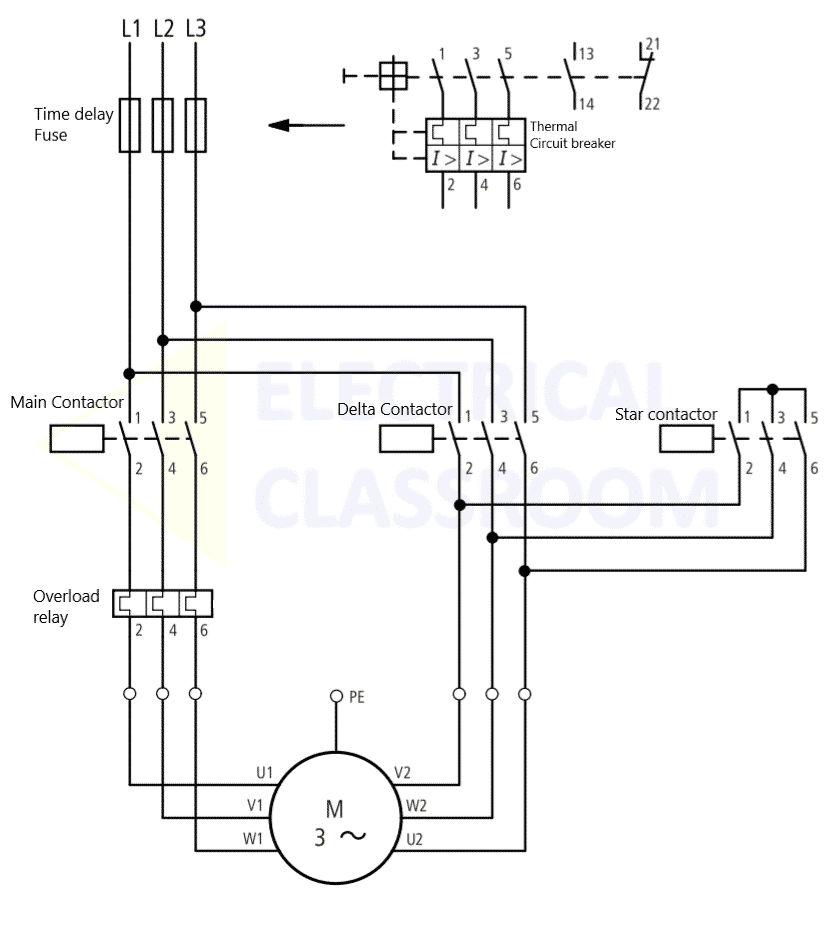
The power circuit of a star-delta starter consists of three contactors, an overload relay, fuse, or circuit breaker.
Let’s calculate the size of contactor, fuses, circuit breaker, and an overload relay for 7.5kW, 415 Volt Three Phase squirrel cage induction motor, motor efficiency 98%, 1480 RPM, Power Factor 0.8.
Calculation
Motor full load Line-current = Motor power in watts / (1.732*Volts*Eff*pf)
Main & Star-delta contactor calculation
A star-delta starter consists of three contactors – The main contactor, the Delta contactor, and the star contactor.
- Main contactor rating = 58%X Full Load Line Current = 7.96A
- Delta contactor rating = 58%X Full Load Line Current = 7.96A
- Star contactor rating = 33%X Full Load Line Current = 4.53A
Making/breaking capacity of contactor = 10 x IFLC= 137A
The contactor must be selected such that its rating is higher than the calculated values.
Read more about making and breaking capacities and utilization categorization.
Overload relay setting
The thermal overload relays are installed next to the main contactor before the motor terminals.
Thermal overload relay setting = 58% of IFLC = 7.96 Amp
Fuse rating calculation
Time delay fuses are more preferred and the rating should not exceed 175% of the full load line current.
Time delay fuse rating for star-delta starter = 1.75 * IFLC = 24A (max)
Circuit Breaker calculation
Inverse current circuit breakers are used to protect motors from short circuits. The circuit breaker rating should not exceed 250% of the full load line current.
Circuit breaker rating for star-delta starter = 2.5 * IFLC = 34.33A
Other calculators
- Synchronous speed calculator
- Torque-power calculator
- Power-torque calculator
- Torque-speed calculator
- Speed-torque calculator
- Induction motor slip
- Motor torque calculator
- Motor FLC calculator
- Motor Locked rotor current calculator
- Number of poles calculator
- DOL Starter Design tool
- Star-Delta Starter design tool
- HP to kW Converter
- kW to Amps Converter
- Amps to kW converter
4 thoughts on “Star-Delta starter design tool | Wye-Delta starter design tool”
Leave a Comment
TRUNG TÂM ĐÀO TẠO PLC ATVN
- Chuyên: Đào tạo lập trình PLC, thiết kế tủ điện, autocad, Robot
- Hotline: 032.868.3266 (zalo) – 0965.682.689 (zalo)
- Địa chỉ: 105 Lai Xá, Kim Chung, Hoài Đức, Hà Nội
- Email: tudonghoaatvn@gmail.com
why do we have to select the circuit breakers 2.5 times more than the FLC of the motor? I used to select the next higher rating of the circuit breakers. But, i did not face any issues so far. For example, I will select a circuit breaker of 16A Type-C MCB, which can tolerate 5 times 16A (80A) instantaneous currents, as the motor’s FCL is 13.73A and the starting current also won’t exceed 3 times the FCL as it is a star-delta starter. Please explain why you have selected 2.5 times the FLC?
Circuit breaker, MCB or MCCB is selected 2.5 times in order to avoid nuisance trips. As you mentioned, the current will not exceed 3 times the FLC. If you refer to the trip curve of MCB if the current is 3 times the rated current for 5 sec, the circuit breaker will trip. In some applications such as that of crushers, this would result in nuisance trips.
Please in My plant we have compressors that are on Star-Delta starters and the specs on compressors motors are: 3 Phase voltage= 460v, 150 KW, PF=0.86, Efficiency = 93.8, FLC = 230AMPS, 200HP. Name plate information.
These compressors are currently protected by six 200Amps time delay fuses. My question is, should these fuses be 1.75×230 amps= 402.5 amps fuses?
450A time delay fuse can fulfill your requirement. FRS-R (600 V) Class RK5 Fusetron™ – FRS-R-450 would be the right choice.